Table of Contents
Tunnel Gantry
NPEC Tunnel Formworks or Tunnel Gantry is the most admired product of ours. We have fabricated various Tunnel Formworks till date starting from 3.3mtr dia to 20mtr diameter. Our range includes complete mechanical gantry, complete hydraulic gantry or a combination of mechanical and hydraulic formworks. The shape is as per the requirement of the project namely Horse Shoe Gantry , Modified Horse Shoe Gantry, D type Gantry , Bellmouth gantry and also special gantries for various locations in the tunnel like Cavern Gantry, Pocket Gantry, T junction or Y junction Gantry etc.
NPEC: Delivering Efficiency with Top-Tier Tunnel Lining Gantries
National Power Engineering Company (NPEC), a leading name in Siliguri’s construction industry, takes immense pride in offering innovative solutions to streamline your tunnelling projects. One of the most critical aspects of tunnel construction is the creation of a strong, smooth, and durable concrete lining. This lining acts as the backbone of the tunnel, ensuring its long-term stability and functionality. Here at NPEC, our expertise in tunnel lining gantries empowers you to achieve precisely that – efficient and high-quality tunnel construction.
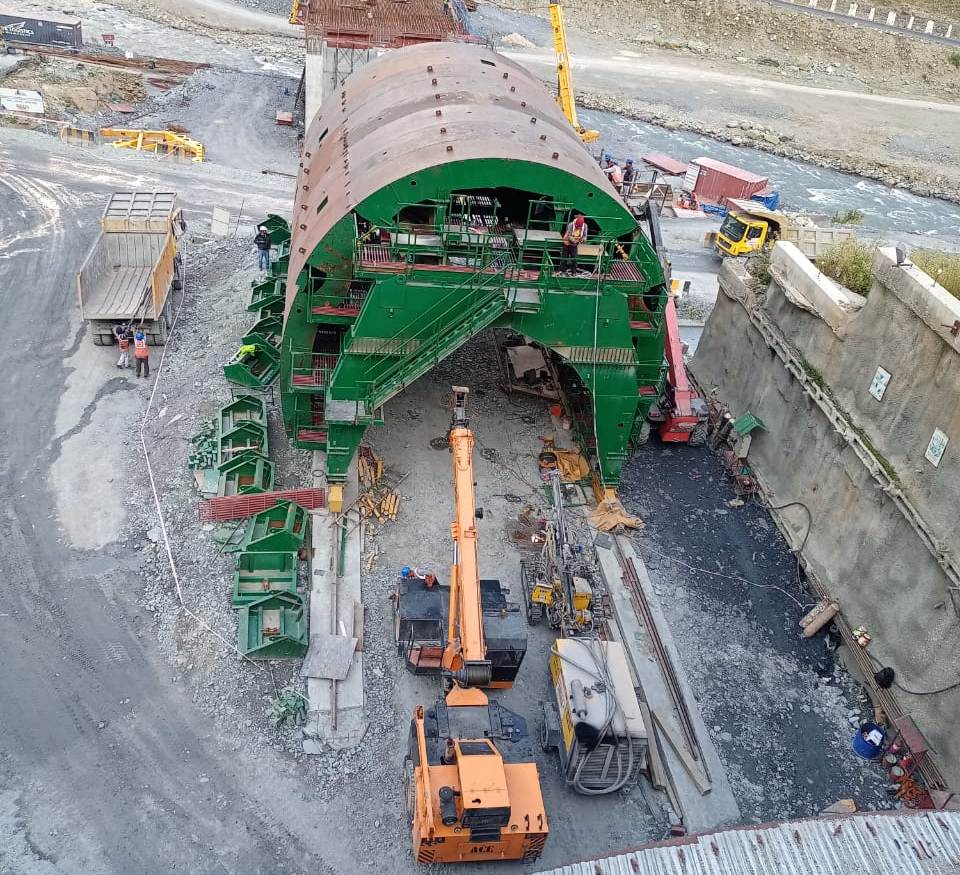
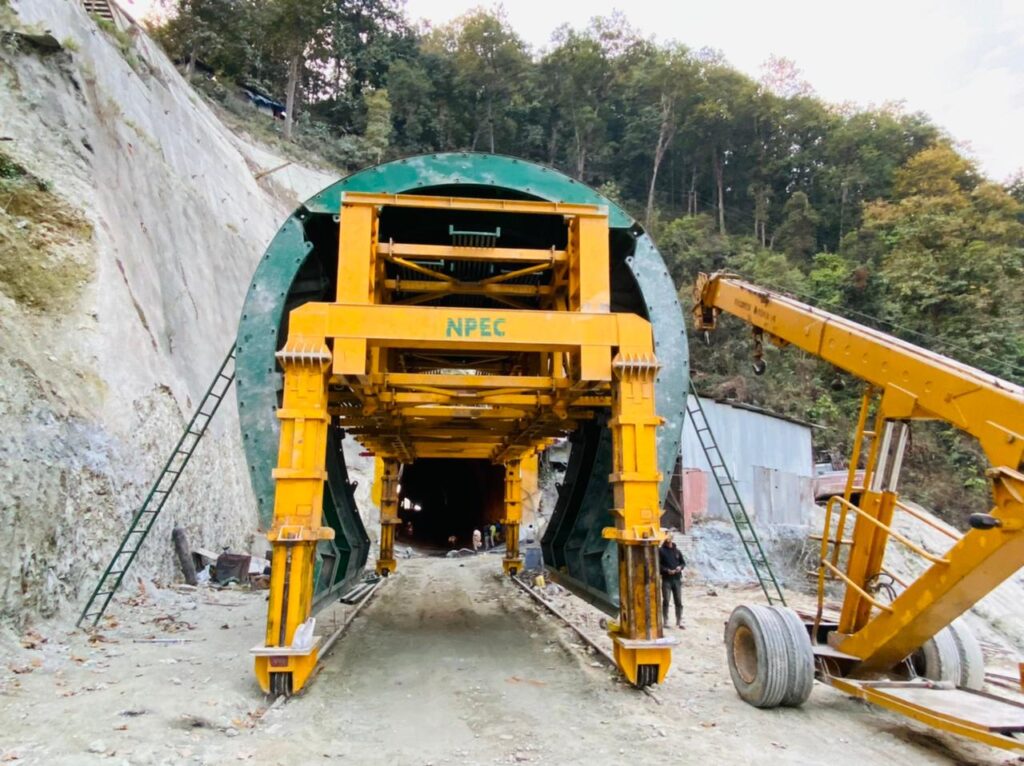
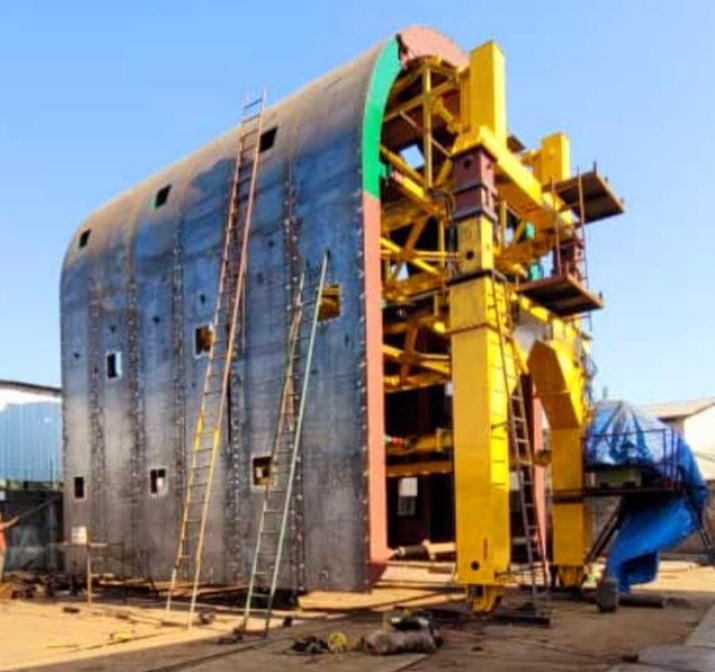

Understanding Tunnel Lining Gantries
Imagine a giant, adaptable mould specifically designed for shaping concrete within a tunnel excavation. That’s essentially what a tunnel lining gantry, also known as tunnel formwork, is. These remarkable pieces of equipment play a pivotal role in the construction process. They provide the framework for the wet concrete, guiding it into the desired tunnel profile. NPEC’s tunnel lining gantries are renowned for their:
- Unmatched Durability: Constructed from high-grade steel, they can withstand the rigors of even the most demanding tunnel environments. The robust design ensures the gantry maintains its structural integrity throughout the pouring and curing process.
- Unwavering Versatility: NPEC understands that no two tunnels are identical. That’s why we offer a wide range of gantry options to accommodate various tunnel shapes and sizes. Whether you are working on a small utility tunnel or a large-scale infrastructure project, we have the right gantry to fit your needs.
- Streamlined Efficiency: NPEC’s tunnel lining gantries are designed with ease of use in mind. They can be assembled, disassembled, and moved quickly within the tunnel, minimizing downtime and maximizing productivity during construction.
- Precision Concrete Placement: The meticulous design and robust construction of our gantries ensure accurate concrete placement. This translates to a smooth and high-quality tunnel lining, reducing the need for extensive post-construction rectification work.
By incorporating NPEC’s tunnel lining gantries into your project, you are not just acquiring a piece of equipment; you are investing in efficiency, safety, and superior quality. In the next section, we will delve deeper into the diverse range of tunnel lining gantries offered by NPEC to cater to your specific project requirements.
The Powerhouse of Tunnelling: Unveiling Tunnel Lining Gantries with NPEC
Tunnelling projects are marvels of modern engineering, carving pathways through mountains and beneath cities. But the true strength of a tunnel lies not just in the excavation itself, but in the creation of a strong and smooth concrete lining. This crucial element ensures the tunnel’s long-term stability and functionality. Here at NPEC, we play a vital role in achieving this with our expertise in tunnel lining gantries.
Demystifying the Tunnel Lining Gantry:
Imagine a massive, adaptable mould specifically designed for a tunnel environment. This is the essence of a tunnel lining gantry, also known as tunnel formwork. These ingenious pieces of equipment act as the guiding force for the concrete within the tunnel excavation. Think of pouring wet concrete; the gantry acts as a framework, shaping the concrete into the desired tunnel profile. NPEC’s tunnel lining gantries are renowned for their:
- Unmatched Durability: Built to endure the harsh realities of tunnel construction, our gantries are crafted from high-grade steel. This robust design ensures they can withstand the immense pressure and weight of the concrete during the pouring and curing process.
- Tailored Versatility: NPEC recognizes that the world of tunnels is as diverse as its applications. Unlike a one-size-fits-all approach, we offer a comprehensive range of gantry options. These cater to a wide variety of tunnel shapes and sizes, from the relatively small utility tunnels to the expansive infrastructure projects that form the backbone of modern transportation networks. No matter the project’s scale, NPEC has the right gantry to fit your specific needs.
- Streamlined Efficiency: Time is money, especially in large-scale construction projects. That’s why NPEC’s tunnel lining gantries are designed with user-friendliness in mind. They boast features that facilitate quick assembly, disassembly, and movement within the tunnel. This minimizes downtime during construction, allowing you to maximize productivity and keep your project on schedule.
- Precision Poured, High-Quality Finish: The meticulous design and robust construction of our gantries go hand-in-hand to ensure accurate concrete placement. This translates to a smooth and high-quality tunnel lining. By minimizing concrete inconsistencies and imperfections, you reduce the need for extensive post-construction rectification work, saving both time and resources.
Incorporating NPEC’s tunnel lining gantries into your project goes beyond acquiring a piece of equipment. It’s an investment in efficiency, safety, and ultimately, the superior quality of your finished tunnel. In the following section, we’ll delve deeper into the diverse range of tunnel lining gantries offered by NPEC, ensuring you have the perfect solution for your specific tunnelling project.
Types of Tunnel Lining Gantries offered by NPEC
At NPEC, we understand that a one-size-fits-all approach doesn’t work in tunnel construction. That’s why we offer a diverse range of tunnel lining gantry options to cater to the specific requirements of your project. Here’s a detailed look at some of our most popular gantry types:
- Horse-Shoe Gantry: As the name suggests, this is the most widely used type of tunnel lining gantry. It’s specifically designed for creating the traditional horseshoe-shaped tunnel profile commonly encountered in transportation and utility applications. The robust design of the horse-shoe gantry ensures efficient and precise concrete placement, resulting in a structurally sound and smooth tunnel lining.
- Modified Horse-Shoe Gantry: This gantry builds upon the strengths of the standard horse-shoe design while offering additional flexibility.It allows for the incorporation of specific features directly into the formwork.For instance, recesses can be integrated into the gantry to accommodate ventilation ducts or cable trays during the concrete pouring stage.This eliminates the need for additional post-construction work, saving time and cost.
- D-Type Gantry: Not all tunnels are circular. For rectangular or square-shaped tunnels frequently used in stations, shafts, and basements, NPEC offers the D-Type gantry.This gantry system provides a stable and secure formwork solution for these non-circular geometries.Similar to the horse-shoe gantry, the D-Type gantry ensures accurate concrete placement, leading to a high-quality finished product.
- Bellmouth Gantry: Tunnels don’t just disappear underground; they eventually need to transition to the open air.This transition zone at the entrance and exit of a tunnel presents a unique challenge. NPEC’s bell mouth gantry is specifically designed to address this need. It facilitates the smooth tapering of the circular tunnel section towards the open excavation, ensuring a seamless and structurally sound transition for the entire tunnel structure.
Beyond these standard offerings, NPEC prides itself on its ability to design and manufacture special gantries for projects with unconventional requirements.This includes gantries for:
- Caverns: Large underground spaces often require extensive and complex formwork solutions. NPEC’s team of engineers can design gantries specifically suited for the unique geometries and dimensions of caverns.
- Pockets: Smaller excavations branching off from the main tunnel may necessitate specialized formwork. NPEC can create gantries that can be maneuvered and positioned effectively within these confined spaces.
- T-junctions and Y-junctions: Where tunnels intersect, creating a structurally sound connection is crucial. NPEC’s specially designed gantries for T-junctions and Y-junctions ensure precise concrete placement at these critical points, guaranteeing the integrity of the entire tunnel network.
Benefits of Using NPEC’s Tunnel Lining Gantries
Choosing NPEC’s tunnel lining gantries offers several advantages for your project:
- Improved Construction Speed: Our efficient design allows for faster deployment and movement of the gantry, leading to quicker completion of the concrete lining.
- Enhanced Safety: The robust construction and secure locking mechanisms ensure worker safety throughout the operation.
- Superior Quality Finish: The precise design and high-quality materials guarantee a smooth and consistent concrete finish, minimizing the need for post-construction rectification work.
- Reduced Labor Costs: The user-friendly design minimizes the manpower required for assembly, operation, and disassembly, lowering labour costs.
- Cost-Effectiveness: NPEC’s gantries are built for long-lasting use, reducing the need for frequent replacements and ensuring a high return on investment.
NPEC’s Commitment to Quality and Service
At NPEC, we understand the critical role tunnel lining gantries play in the success of your project. That’s why we are committed to providing:
- Top-notch Quality: We utilize high-grade steel and employ stringent quality control measures to ensure the durability and reliability of our gantries.
- Experienced Engineering Team: Our team of qualified engineers possesses extensive knowledge of tunnel construction and can design gantries that meet your project’s specific requirements.
- Exceptional Customer Service: We provide comprehensive support throughout the project lifecycle, from initial consultation to after-sales service.
NPEC is your one-stop solution for all your tunnel lining gantry needs in Siliguri and beyond. We offer a complete package, including:
- Design and Engineering: Our engineers will work closely with you to design a gantry that perfectly fits your tunnel profile and specifications.
- Fabrication: Utilizing advanced manufacturing techniques, we ensure the highest quality standards in the construction of your gantry.
- Delivery and Erection: NPEC will handle the safe and efficient delivery and assembly of the gantry on your project site.
- Operational Training: Our team will provide comprehensive training to your crew on the proper operation and maintenance of the gantry.
Some of the advantages of using NPEC tunnel formworks are
1. Light weight yet very robust.
2. Very fast delivery cycle.
3. Our technician installs the gantry and educates the client in its operation and maintenance.
4. Moc1. Self propelled hydraulic tunnel formwork
2. Horse shoe hydraulic/mechanical tunnel gantry
3. D type hydraulic/mechanical tunnel gantry
4. Cavern tunnel gantry
5. Modified horse shoe hydraulic tunnel gantry
6. Pocket tunnel gantry
7. T junction tunnel gantry
8. Y junction tunnel gantry
9. Bellmouth tunnel gantry
10 Mechanical tunnel formwork 11 Box Culvert Gantryk assembly is done at works and hence very fast installation at site.
5. After sales support is very prompt.
6. Best hydraulic components are used which guarantees trouble free operation for years.
7. Every system has a double lock and hence very safe.
8. In house Structural and Hydraulic design team.
The fact that our Tunnel Gantry is the most preferred choice for our customers, our customers demand for various accessories that is required in Tunnel Works. Till date we have fabricated thousands of tons of LATTICE GIRDERS and RIBS for various tunnel projects. The Ribs have been made from ISMB 150, ISMB 200, ISMB 250 and ISHB 200 sections. Apart from this we have manufactured various types of ROCK BOLTS and ANCHOR BOLTS and BEARING PLATES. At times tunnels require STEEL Ducting for air circulation. We have fabricated more than 50Km of Steel Ducting till date for various projects.

NPEC: Leaders in Tunnel Gantry Systems
In the intricate realm of tunnel construction, where precision meets complexity, the role of gantry systems is paramount. Among the pioneers shaping this landscape stands New Paradigm Engineering Corporation (NPEC), a trailblazer renowned for its innovation and expertise in designing and manufacturing gantry systems tailored specifically for tunnel construction projects.
Origins of Excellence
Founded on the principles of innovation and engineering excellence, NPEC embarked on its journey, driven by a vision to revolutionize tunnel construction methodologies. Since its inception, the company has remained steadfast in its commitment to pushing the boundaries of technological advancement and delivering solutions that redefine industry standards.
Engineering Ingenuity
At the heart of NPEC’s success lies its unwavering dedication to engineering ingenuity. The company boasts a team of seasoned experts, comprising engineers, designers, and technicians, who collectively possess a wealth of experience and expertise in the field of gantry system design and manufacturing. Leveraging state-of-the-art technologies and cutting-edge methodologies, NPEC’s engineering team consistently delivers innovative solutions tailored to meet the unique challenges of tunnel construction projects.
Customized Solutions
One of NPEC’s defining strengths lies in its ability to offer customized solutions that address the specific needs and requirements of each individual project. Recognizing that no two tunnel construction projects are alike, NPEC collaborates closely with clients to develop gantry systems that are precisely tailored to their unique circumstances. Whether it’s a high-speed rail tunnel, an underground transportation network, or a utility tunnel, NPEC’s bespoke solutions are designed to optimize efficiency, maximize performance, and ensure the successful completion of every project.
Technological Advancements
NPEC’s commitment to innovation is evident in its continuous pursuit of technological advancements. The company invests heavily in research and development, constantly exploring new technologies and methodologies to enhance the performance, reliability, and safety of its gantry systems. From advanced automation and robotics to real-time monitoring and predictive maintenance, NPEC’s gantry systems are equipped with the latest advancements, ensuring optimal performance and efficiency on every project.
Global Reach, Local Expertise
While NPEC’s headquarters may be located [insert location], its impact extends far beyond national borders. With a global network of partners, distributors, and service centres, NPEC serves clients across the globe, providing unparalleled expertise and support throughout every stage of the project lifecycle. Despite its global reach, NPEC remains firmly rooted in its commitment to local communities and environments, adhering to the highest environmental and sustainability standards in its operations.
As a leading manufacturer of gantry systems for tunnel construction, NPEC continues to set the standard for excellence in the industry. With a legacy of innovation, engineering ingenuity, and unwavering commitment to customer satisfaction, NPEC remains at the forefront of technological advancement, driving progress and redefining the possibilities of tunnel construction. Whether it’s enhancing efficiency, improving safety, or delivering customized solutions, NPEC stands ready to meet the evolving needs of the industry and exceed the expectations of its clients worldwide.
Unveiling the Ingenious Role of Gantry Systems in Tunnel Construction
In the realm of modern infrastructure, tunnels stand as a testament to human ingenuity, enabling efficient passage through obstacles that once seemed insurmountable. Behind the scenes of these subterranean marvels lies a symphony of engineering precision, where every element must align with exactitude to ensure safety, durability, and functionality. Among the array of specialized equipment employed in tunnel construction, gantry systems emerge as unsung heroes, orchestrating the intricate dance of materials and machinery to bring these underground passages to life. In this exploration, we delve into the multifaceted role of gantry systems in tunnel construction, unveiling their significance, functionality, and innovative applications.
The Essence of Gantry Systems in Tunnel Construction
At its core, a gantry system represents a framework of steel or reinforced concrete, strategically designed to support heavy loads and provide a stable platform for various construction activities within a tunnel. These versatile structures serve as the backbone of tunnel construction projects, facilitating the movement of equipment, materials, and personnel while ensuring safety and efficiency in challenging underground environments.
Gantry systems in tunnel construction typically comprise several key components, each playing a crucial role in the execution of construction tasks:
1. Main Structure: The main structure of a gantry system forms the framework upon which all other components are mounted. Constructed from high-strength materials such as steel or reinforced concrete, the main structure provides stability and support, allowing for the safe operation of machinery and equipment within the tunnel.
2. Gantry Crane: Central to the functionality of a gantry system is the gantry crane, a robust lifting apparatus capable of hoisting heavy loads with precision and control. Equipped with hoists, winches, or hydraulic systems, gantry cranes are essential for tasks such as transporting construction materials, installing tunnel segments, and facilitating maintenance operations within the tunnel.
3. Rail System: Many gantry systems utilize a rail system embedded within the tunnel floor, allowing for smooth and controlled movement of the gantry crane along predefined tracks. These rail systems enable precise positioning of the gantry crane, ensuring optimal access to different areas of the tunnel during construction.
4. Control System: The control system serves as the nerve centre of the gantry system, overseeing its operation and coordination of various components. Modern gantry systems are equipped with advanced control interfaces that allow operators to monitor performance parameters, adjust settings, and respond to real-time feedback to ensure safe and efficient operation.
5. Safety Features: Safety is paramount in tunnel construction, and gantry systems are equipped with a range of safety features to mitigate risks and protect workers and equipment. These features may include overload protection mechanisms, emergency stop buttons, and automated monitoring sensors that detect potential hazards and prompt immediate action to prevent accidents.
Functionality and Applications of Gantry Systems in Tunnel Construction
The functionality and versatility of gantry systems make them indispensable tools in tunnel construction, facilitating a wide range of tasks across various stages of the project lifecycle. From initial excavation to final lining installation, gantry systems play a vital role in ensuring the success and efficiency of tunnel construction projects. Some key applications of gantry systems in tunnel construction include:
1.Excavation Support: During the initial stages of tunnel construction, gantry systems are often employed to provide support for excavation activities. Gantry cranes equipped with specialized attachments, such as drilling rigs or rock bolting machines, assist in stabilizing tunnel walls, reinforcing rock formations, and removing debris to create a safe working environment for construction crews.
2. Segment Handling and Installation: In the construction of lined tunnels, gantry systems play a crucial role in handling and installing tunnel segments or lining elements. Gantry cranes equipped with precision lifting mechanisms are used to transport precast concrete segments into the tunnel and precisely position them to form the tunnel lining. This process requires meticulous coordination and accuracy to ensure the structural integrity and longevity of the tunnel.
3. Formwork and Concrete Pouring: Gantry systems are also utilized in formwork and concrete pouring operations, particularly in the construction of tunnel walls, floors, and ceilings. Gantry cranes fitted with formwork assemblies facilitate the creation of moulds or templates for pouring concrete, while precise control systems ensure uniform distribution and consolidation of concrete to achieve the desired structural strength and finish.
4. Utility Installation and Maintenance: Beyond structural elements, gantry systems are instrumental in the installation and maintenance of utilities within tunnels, such as electrical conduits, ventilation ducts, and piping systems. Gantry cranes equipped with specialized attachments enable the precise positioning and installation of utility components, while advanced control systems ensure compatibility with existing infrastructure and adherence to safety standards.
5. Emergency Response and Rescue Operations: In the event of emergencies or incidents within the tunnel, gantry systems play a critical role in facilitating emergency response and rescue operations. Gantry cranes equipped with rescue hoists, stretchers, and other specialized equipment enable rapid extraction of injured personnel or removal of obstacles obstructing access to critical areas of the tunnel, helping to mitigate risks and minimize downtime.
Innovative Advancements in Gantry Technology
The evolution of gantry technology in tunnel construction has been marked by a continuous quest for innovation and efficiency, driven by advancements in materials, automation, and digitalization. Some notable innovations shaping the future of gantry systems in tunnel construction include:
1. Advanced Materials and Lightweight Design: The use of advanced materials such as carbon fibre composites and high-strength alloys has enabled the development of lightweight gantry structures that offer enhanced strength and durability while minimizing weight and footprint. These lightweight gantry systems are easier to transport, assemble, and manoeuvre within confined tunnel spaces, allowing for greater flexibility and efficiency in construction operations.
2. Robotics and Automation: The integration of robotics and automation technologies has revolutionized gantry operations, enabling greater precision, productivity, and safety in tunnel construction. Robotic gantry systems equipped with autonomous navigation capabilities, sensor-based control systems, and adaptive algorithms can perform complex tasks with minimal human intervention, reducing the risk of accidents and improving overall project efficiency.
3. Digital Twin and Simulation Modelling: The concept of digital twin and simulation modelling has gained traction in gantry technology, allowing engineers to create virtual replicas of gantry systems and simulate their behaviour in various operating conditions. Digital twin models enable predictive analysis, optimization, and troubleshooting of gantry operations, facilitating better decision-making and performance management throughout the project lifecycle.
4. Remote Monitoring and Telemetry: Remote monitoring and telemetry systems enable real-time monitoring of gantry performance parameters, such as load capacity, operating temperature, and vibration levels, from a centralized control centre. These systems provide valuable insights into gantry operation, enabling proactive maintenance, troubleshooting, and optimization to ensure optimal performance and reliability.
5. Augmented Reality and Virtual Reality: Augmented reality (AR) and virtual reality (VR) technologies are being increasingly utilized in gantry operations to enhance situational awareness, training, and collaboration among construction crews. AR/VR-based training simulations allow operators to familiarize themselves with gantry controls and procedures in a realistic virtual environment, while AR overlays provide real-time visualizations of critical data and instructions during gantry operation, improving efficiency and safety on construction sites.
Gantry Systems – Engineering Excellence Underground
Gantry systems represent indispensable tools in the arsenal of tunnel construction, enabling the safe, efficient, and precise execution of a wide range of construction activities in challenging underground environments. From excavation support to segment installation, utility deployment, and emergency response, gantry systems play a multifaceted role in shaping the landscape of modern infrastructure, connecting communities, and fostering economic development around the globe. As technological advancements continue to push the boundaries of innovation, gantry systems will remain at the forefront of tunnel construction, driving progress, and excellence in engineering underground.