Steel Bridge Fabrication: Building Foundations for Sustainable Infrastructure
Steel bridge fabrication is a complex and highly specialized process that plays a pivotal role in the construction of modern, robust, and sustainable infrastructure. As a cornerstone of civil engineering, steel bridges stand as iconic structures that connect communities, facilitate commerce, and overcome geographical obstacles. In this comprehensive exploration, we delve into the intricate world of steel bridge fabrication, uncovering the key processes, materials, and innovations that contribute to the creation of these vital components of our transportation networks.
Table of Contents
Understanding Steel Bridge Fabrication
The Significance of Steel in Bridge Construction:
Steel has long been the material of choice for bridge construction due to its exceptional strength, durability, and versatility. In steel bridge fabrication, various grades of steel are utilized to meet specific design requirements, ensuring that the resulting structures can withstand the diverse challenges presented by environmental conditions and heavy traffic loads.
Fabrication as a Key Phase in Bridge Construction:
Steel bridge fabrication is a critical phase in the overall bridge construction process. It involves the transformation of raw steel materials into the intricate components that will compose the bridge’s superstructure and substructure. The success of the entire bridge project hinges on the precision and quality achieved during the fabrication stage.
Key Processes in Steel Bridge Fabrication
Material Preparation:
The process begins with material preparation. Steel, typically received in the form of beams, plates, and structural shapes, undergoes thorough inspection and cleaning. Any imperfections or contaminants are meticulously addressed to ensure the highest quality and integrity of the final product.
Cutting and Shaping:
Precision cutting is paramount in steel bridge fabrication. Advanced cutting technologies, such as laser cutting and plasma cutting, are employed to shape steel components according to the project’s specifications. Computer Numerical Control (CNC) machines ensure accuracy, allowing for complex shapes and intricate details.
Welding:
Welding is a fundamental process in steel bridge fabrication, where individual steel components are joined together to form the bridge’s structure. Skilled welders use various welding techniques, including arc welding and gas metal arc welding, to create robust connections that meet stringent engineering standards.
Forming and Assembly:
Forming and assembly involve shaping and fitting the various components into their final configurations. This phase requires meticulous attention to detail to ensure that each part aligns with the design specifications. Large sections of the bridge, such as trusses and girders, are assembled in this stage.
Surface Treatment:
To enhance durability and protect against corrosion, the fabricated steel components undergo surface treatment. This may involve processes such as abrasive blasting, galvanization, or the application of protective coatings. Surface treatment plays a crucial role in extending the lifespan of the steel bridge and reducing maintenance requirements.
Innovations in Steel Bridge Fabrication:

Advanced Materials:
Ongoing innovations in steel bridge fabrication include the development of advanced materials, such as high-strength low-alloy (HSLA) steel and weathering steel. These materials offer improved strength, corrosion resistance, and durability, contributing to the longevity and sustainability of steel bridges.
Automation and Robotics:
Automation and robotics have transformed the steel fabrication industry. Computer-controlled machinery and robotic systems enhance efficiency, precision, and safety in the fabrication process. Automated welding systems, for example, ensure consistent weld quality and reduce the reliance on manual labor.
Building Information Modelling (BIM):
The adoption of Building Information Modelling (BIM) in steel bridge fabrication allows for comprehensive digital representation and simulation of the entire bridge structure. BIM facilitates better collaboration among project stakeholders, minimizes errors, and optimizes the overall fabrication process.
Prefabrication and Modular Construction:
Prefabrication involves assembling components off-site before transporting them to the construction site. This approach enhances efficiency, reduces on-site labour requirements, and accelerates project timelines. Modular construction, incorporating prefabricated components, is increasingly employed in steel bridge fabrication for its advantages in quality control and cost-effectiveness.
Quality Assurance in Steel Bridge Fabrication
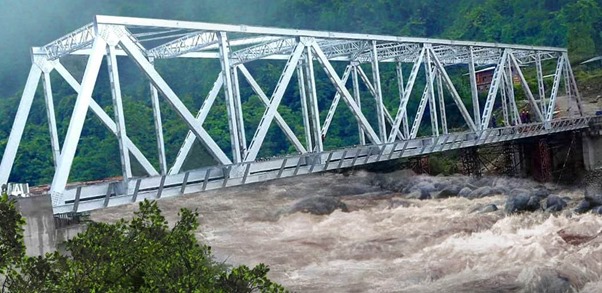
Industry Standards and Codes:
Quality assurance is paramount in steel bridge fabrication, and adherence to industry standards and codes is non-negotiable. Engineers and fabricators must comply with specifications set forth by organizations such as the American Institute of Steel Construction (AISC) in the United States or the European Committee for Standardization (CEN) in Europe.
Non-Destructive Testing (NDT):
Non-destructive testing methods, including ultrasonic testing and magnetic particle inspection, are employed to assess the integrity of welded joints and detect any potential defects. These techniques ensure that the fabricated steel components meet the required quality and safety standards.
Inspection and Quality Control:
Rigorous inspection and quality control processes are implemented throughout steel bridge fabrication. Skilled inspectors examine every stage of the fabrication process, from material preparation to final assembly, to verify compliance with design specifications and industry standards.
Steel bridge fabrication stands as a testament to the intersection of engineering precision, technological innovation, and the enduring strength of steel as a construction material. As the demand for sustainable and resilient infrastructure continues to grow, the evolution of steel bridge fabrication remains at the forefront, shaping the skylines of cities and connecting communities for generations to come. The meticulous processes, advanced materials, and innovations embraced in steel bridge fabrication ensure that these vital structures not only endure but also contribute to the sustainable development of our modern world.
NPEC’s Engineering Excellence: Bhutan Steel Bridge Fabrication
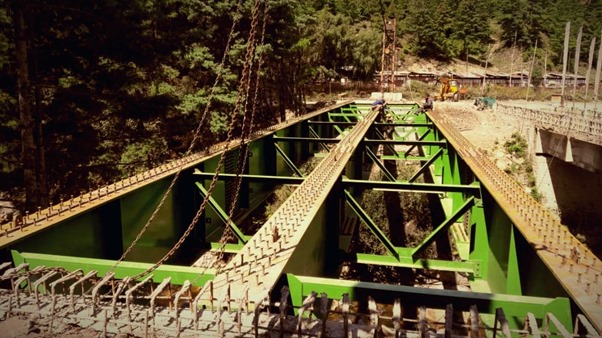
National Power Engineering Company (NPEC), established in Siliguri, West Bengal, has positioned itself as a beacon of engineering innovation, transcending geographical boundaries to contribute to infrastructure development across the region. A testament to NPEC’s prowess is its involvement in the Bhutan Steel Bridge Fabrication project, where precision, adaptability, and a commitment to quality have converged to create resilient structures that span the picturesque landscapes of Bhutan. In this in-depth exploration, we unravel the intricacies of NPEC’s involvement in Bhutan’s steel bridge fabrication, showcasing the company’s dedication to engineering excellence.
1. NPEC’s Presence in Bhutan:
NPEC’s foray into Bhutan exemplifies its commitment to cross-border collaborations and its vision to contribute to the infrastructural growth of neighbouring nations. Bhutan, nestled in the eastern Himalayas, presented unique challenges and opportunities for engineering firms, and NPEC’s expertise was strategically employed to address the intricate requirements of steel bridge fabrication in this awe-inspiring landscape.
2. Geographical Challenges and Adaptability:
Bhutan’s diverse topography, characterized by steep valleys and mountainous terrains, demanded a high degree of adaptability in engineering solutions. NPEC’s engineers, well-versed in working with challenging landscapes, embraced the unique challenges posed by Bhutan’s geography. The Bhutan Steel Bridge Fabrication project required not only technical proficiency but also an acute understanding of the environmental and geological factors influencing the construction process.
3. Tailoring Solutions to Bhutan’s Needs:
One of NPEC’s key strengths lies in its ability to tailor solutions to the specific needs of each project. In the context of Bhutan’s steel bridge fabrication, this meant a meticulous examination of the local environmental conditions, seismic considerations, and the load-bearing requirements of the bridges. The company’s engineers collaborated closely with Bhutanese authorities to understand the nuances of the terrain, ensuring that the fabricated bridges would not only meet but exceed the standards of resilience required in this seismic zone.
4. Precision Engineering in Bhutan’s Steel Bridge Fabrication:
Material Selection:
The foundation of any steel bridge fabrication project lies in the selection of materials. In Bhutan, where environmental conditions vary from sub-tropical in the southern plains to alpine in the northern regions, NPEC’s engineers carefully chose materials resilient to corrosion and capable of withstanding the diverse climatic conditions. High-strength steel alloys were employed, ensuring the bridges could endure both the tropical heat and the alpine cold.
Advanced Cutting and Shaping Techniques:
Precision cutting is integral to steel bridge fabrication, and in Bhutan, where landscapes can be rugged and access challenging, advanced cutting and shaping techniques became imperative. NPEC leveraged cutting-edge technologies, including laser cutting and plasma cutting, to shape steel components with precision, ensuring that each element met the exacting standards required for seamless assembly.
Welding Expertise:
Welding, a critical process in bridge fabrication, demands not only skilled craftsmanship but also an understanding of the structural integrity required for bridges in seismic zones. NPEC’s welders, trained to the highest standards, employed advanced welding techniques to create robust connections capable of withstanding both static and dynamic loads.
Forming and Assembly Challenges:
The unique topography of Bhutan posed challenges in forming and assembling large bridge sections. NPEC’s engineers adeptly navigated these challenges, developing innovative solutions for on-site assembly. Prefabrication techniques were employed to streamline the construction process, minimizing on-site labor requirements and accelerating project timelines without compromising quality.
Surface Treatment for Longevity:
Bhutan’s varying climates and altitudes necessitated a meticulous approach to surface treatment. NPEC implemented comprehensive surface treatment processes, including galvanization and protective coatings, to enhance the longevity of the steel components. This strategic approach is aimed at minimizing maintenance requirements and ensuring the sustained resilience of the fabricated bridges.
5. Innovations in Bhutan’s Steel Bridge Fabrication:
Environmental Considerations:
Bhutan’s commitment to environmental conservation aligned seamlessly with NPEC’s ethos. The steel bridge fabrication project integrated environmentally conscious practices, such as recycling and sustainable material sourcing, minimizing the ecological footprint of the construction process.
Seismic Resilience Innovations:
Recognizing Bhutan’s seismic vulnerability, NPEC incorporated innovative seismic resilience features into the bridge designs. The engineering team implemented base isolators, dampers, and other seismic retrofitting techniques to enhance the bridges’ ability to withstand earthquakes and ensure the safety of the infrastructure.
Collaboration with Local Communities:
NPEC’s approach to the Bhutan Steel Bridge Fabrication project extended beyond technical excellence. The company actively engaged with local communities, fostering collaboration, and incorporating traditional knowledge into the engineering solutions. This collaborative approach not only enriched the project but also ensured that the bridges seamlessly integrated into the cultural and social fabric of Bhutan.
6. Quality Assurance and Inspection:
Adherence to International Standards:
Quality assurance is a hallmark of NPEC’s operations, and the Bhutan Steel Bridge Fabrication project was no exception. The company adhered to international standards and codes, aligning with organizations such as the American Institute of Steel Construction (AISC) and incorporating best practices from global engineering norms.
Rigorous Inspection Protocols:
Rigorous inspection protocols were implemented at every stage of the Bhutan steel bridge fabrication process. Skilled inspectors meticulously examined the fabricated components, ensuring that each element met the design specifications and complied with the stringent quality and safety standards set forth for the project.
Non-Destructive Testing (NDT):
Non-destructive testing techniques, including ultrasonic testing and magnetic particle inspection, were employed to assess the integrity of welds and detect potential defects. These advanced testing methods ensured that the fabricated bridges met the highest standards of safetyand structural robustness.
7. Project Execution and Impact:
The successful execution of NPEC’s Bhutan Steel Bridge Fabrication project marked a significant milestone in the region’s infrastructure development. The fabricated bridges, standing as engineering marvels, not only facilitated seamless connectivity but also contributed to the socio-economic growth of Bhutan. The project’s impact extended beyond its structural achievements, fostering a spirit of collaboration, knowledge exchange, and sustainable development.
8. Future Prospects and Continued Collaboration:
NPEC’s foray into Bhutan’s steel bridge fabrication has set the stage for continued collaboration and future prospects in the region. The success of the project has reinforced NPEC’s reputation as a trusted partner in the development of resilient and sustainable infrastructure, and the company remains poised to contribute to the evolving needs of Bhutan and neighbouring nations.
NPEC’s Bhutan Steel Bridge Fabrication project stands as a testament to the company’s commitment to engineering excellence, adaptability, and innovation. The intricacies of working in the challenging terrain of Bhutan were met with precision and expertise, resulting in resilient bridges that seamlessly integrate with the natural beauty of the landscape. As NPEC continues to pioneer advancements in the field of engineering, the Bhutan Steel Bridge Fabricationproject remains a shining example of cross-border collaboration and the transformative impact of infrastructure development on the socio-economic fabric of nations.
Choosing National Power Engineering Company (NPEC) for fabrications, especially in complex and critical projects like steel bridge fabrication, is a decision rooted in a combination of expertise, innovation, and a track record of successful project delivery. Here are compelling reasons why NPEC stands out as the preferred choice for such fabrications:
Engineering Excellence:
NPEC has established itself as a paragon of engineering excellence. The company’s team comprises seasoned professionals, skilled engineers, and experts who bring a wealth of experience to every project. The commitment to precision, innovation, and adherence to the highest engineering standards ensures that projects are executed with utmost proficiency.
Proven Track Record:
NPEC boasts a proven track record of delivering successful projects across various engineering domains. The completion of intricate projects, including steel bridge fabrications, underscores the company’s capability to meet and exceed client expectations. This track record instils confidence in clients seeking a reliable partner for their fabrication needs.
Adaptable Solutions:
The ability to adapt to diverse project requirements is a hallmark of NPEC’s approach. In fabrications where each project presents unique challenges, NPEC’s engineers exhibit flexibility and innovation to tailor solutions that address specific needs. This adaptability ensures that projects are not only executed efficiently but also optimized for the distinct characteristics of each environment.
Technological Innovation:
NPEC remains at the forefront of technological innovation in the engineering industry. The integration of advanced technologies, such as laser cutting, plasma cutting, and automation, enhances the efficiency and precision of fabrications. This commitment to staying abreast of technological advancements positions NPEC as a leader in delivering state-of-the-art solutions.
Comprehensive Services:
NPEC offers comprehensive services that cover the entire project lifecycle. From initial design and material selection to fabrication, quality assurance, and project management, NPEC’s end-to-end services ensure a seamless and integrated approach. Clients benefit from a one-stop solution provider that can manage all aspects of complex fabrications.
Sustainability Focus:
NPEC places a strong emphasis on sustainable engineering practices. This commitment is reflected in material choices, fabrication processes, and project execution strategies. Clients seeking environmentally conscious solutions find NPEC to be a partner aligned with their sustainability goals, ensuring that fabrications contribute to a greener and more sustainable future.
Collaborative Approach:
NPEC adopts a collaborative approach to project execution. Engaging with clients, local communities, and stakeholders is integral to the company’s ethos. This collaborative spirit ensures that the final fabricated structures not only meet technical specifications but also integrate seamlessly into the broader socio-economic and cultural context.
Safety Protocols:
Safety is a top priority for NPEC. Rigorous safety protocols are integrated into every phase of project execution, from material handling to on-site construction. NPEC’s commitment to creating a safe working environment not only protects the well-being of workers but also ensures the durability and reliability of the fabricated structures.
Customer-Centric Philosophy:
NPEC places a premium on client satisfaction. A customer-centric philosophy permeates every aspect of the company’s operations. Clear communication, transparent project management, and a focus on understanding and meeting client expectations contribute to enduring client relationships.
Cross-Border Expertise:
NPEC’s experience in executing projects across borders, as evidenced by its involvement in the Bhutan Steel Bridge Fabrication project, demonstrates the company’s ability to navigate diverse geographical, cultural, and regulatory landscapes. Clients seeking a partner with cross-border expertise find NPEC to be a reliable choice for international projects. Choosing NPEC for fabrications, particularly in intricate and critical projects like steel bridge fabrication, ensures a combination of engineering prowess, technological innovation, and a commitment to client satisfaction. The company’s proven track record, adaptability, and comprehensive services make NPEC a preferred choice for clients seeking reliable and cutting-edge solutions in the field of engineering fabrications.